事故災害の予防に役立つリスクアセスメントとは?概要と進め方を解説
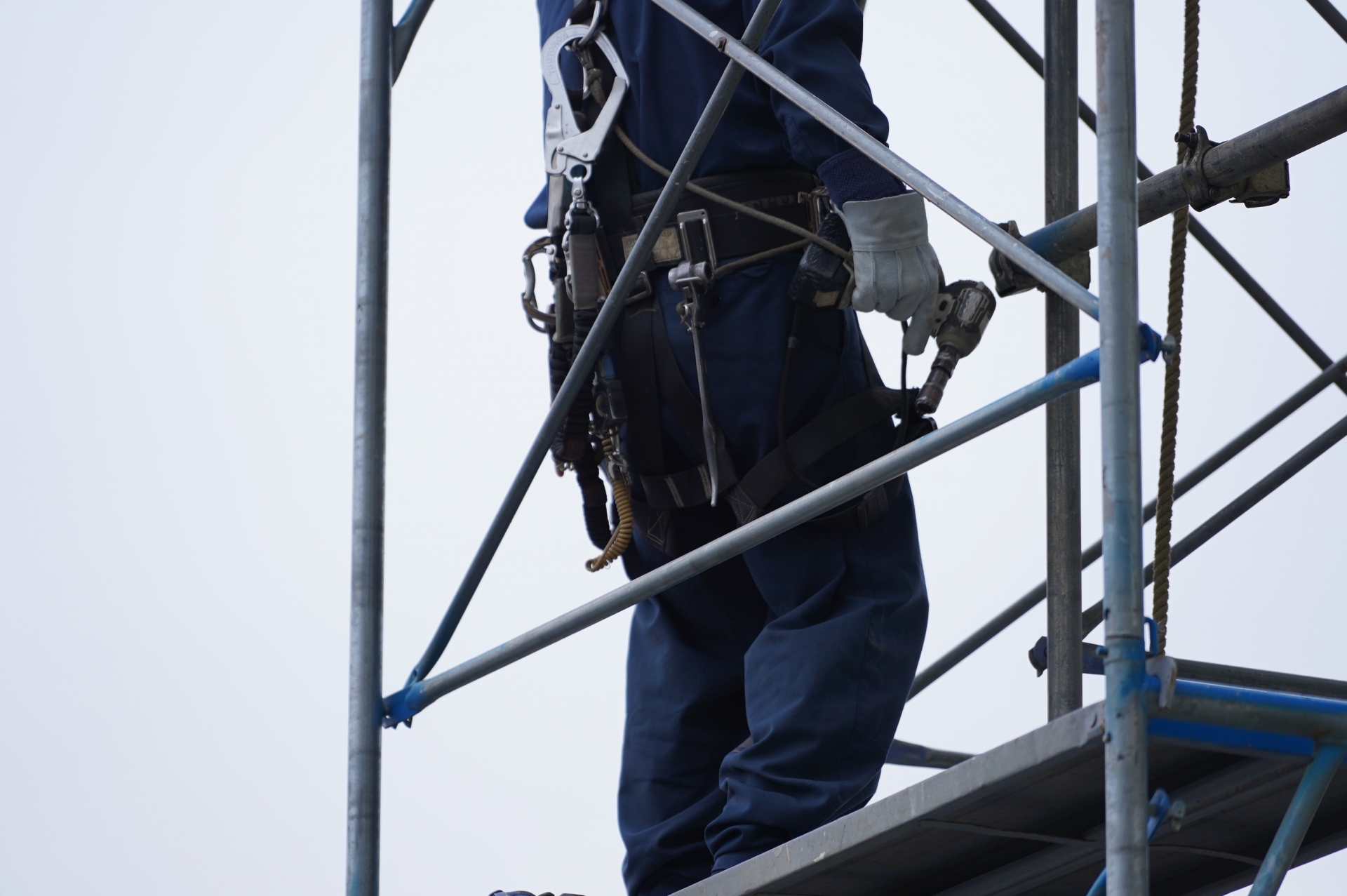
リスクアセスメントは、製造業や建設業などのものづくりに携わる仕事、その他機械や化学、福祉・サービス業などさまざまな業界で必要とされています。
労働災害などのトラブルを防ぐためには、リスクアセスメントを普段から心掛けることが大切です。具体的に、どのようなポイントに注意し、どのように対策を講じるべきなのでしょうか。
この記事では、リスクアセスメントの概要や目的、期待できる効果について詳しく紹介します。リスクアセスメントの進め方や代表的な手法、実際の事例として食料品製造業と木材・木材製品製造業のリスクアセスメントを取り上げています。
リスクアセスメントとは?
「リスクアセスメント」は、日本語にすると「危険の事前評価」と訳される言葉です。
それぞれの職場や作業において、潜在的な危険性や有害性を見つけだし、労働災害や健康障害の可能性・重篤度・被災の程度や可能性を考慮して「リスク」とします。リスクがどの程度の被害や危険をもたらすか、具体的に想定し見積もりを行います。
厚生労働省が公表している「危険性又は有害性等の調査等に関する指針」では、リスクに含める「危険性又は有害性」の分類は以下のとおりです。(※)
危険性 |
|
有害性 |
|
リスクを低減するための方法を複数検討し、優先度をつけます。優先度に応じた措置を順に実施し、措置の結果や措置の内容を記録して、災害を防ぐノウハウとして蓄積します。これらのプロセスが、リスクアセスメントと呼ばれる行動です。
労働災害や健康被害は、さまざまな事業所や作業場で発生するおそれがあります。労働安全衛生法では「危険性又は有害性等の調査及びその結果に基づく措置」として、製造業や建設業等の事業者が、リスクアセスメントとその結果に基づく措置を実施する必要があるとして、努力義務を定めています。
※参照元:厚生労働省安全衛生部安全課「危険性又は有害性等の調査等に関する指針」
リスクアセスメントの目的
リスクアセスメントの目的は、職場や仕事における安全・衛生を確保し、労働災害や健康被害を未然に防ぐことです。
事前にリスクを想定・特定することで予防策を講じられるため、不慮の事故やトラブルを防止できるのです。また、職場環境での安全衛生意識向上にも役立ちます。
技術の革新・進展によって、ものづくりの現場では生産工程が多様化し、複雑化しているといわれています。操作の複雑な機械設備を導入した結果、生産性が向上する一方で労働災害や健康被害のリスクも多様化しています。
リスクアセスメントは多様化する作業環境で個々に危険を把握し、予防するための手段でもあります。具体的にどのような効果が期待できるのでしょうか。
リスクアセスメントを実施することで期待できる効果
リスクアセスメントを実施すると、次の効果が期待できます。
- 職場に潜むリスクを共有できる
- 従業員の安全意識を高める
- 事故の発生リスクを下げる
ここからは、リスクアセスメントによって得られる効果を確認していきましょう。
職場に潜むリスクを共有できる
労働や作業においてどのようなリスクがあるのかを洗い出し、特定・周知ことで、潜在的なリスクを従業員全員が共有できます。
一例として、有害な化学物質を扱う作業場では、化学物質の特性や危険性、事故につながりやすい行動などをまとめたうえで、注意すべきポイントを明らかにします。その情報を従業員全員に共有して注意喚起を行うことで、誤った化学物質の取り扱いを未然に防ぎ、労働災害や健康被害を予防できるという仕組みです。
過去に発生した労働災害や健康被害の内容、同業他社の発災事例を参考にリスクを共有する手法も有効です。今まで意識されていなかった、または見落とされていたリスクを共有することができます。
従業員の安全意識を高める
目の前の作業に取り掛かっているあいだは、災害や事故の発生リスクに気づきにくいものです。そこで、事前にリスクアセスメントを行うことで、従業員一人ひとりや従業員同士での安全意識を高められます。
リスクアセスメントのポイントは、分析者が全員で参加し、管理者から従業員まで全員が同じ認識をもつことです。リスクを明確にして対策をするだけではなく、全員が当事者としての意識をもつことが、トラブルの予防に繋がるのです。
危険な作業や危険物を扱う環境では、過去に発生した災害や事故の事例を周知する方法も意識の向上に役立ちます。方法や取り扱いを誤ると重大な傷病、または命を失うおそれもあると把握することで、安全意識をもちながら業務に取り掛かれるでしょう。
事故の発生リスクを下げる
リスクを従業員全員で共有し、個々の安全意識が向上することで、事故の発生リスクを下げる効果が期待できます。
一人ひとりがリスクを理解し、避けようと予防するようになり、従業員同士の声掛けや情報共有の機会も生まれます。
これまで、労働災害や健康被害を防止する方法は事故が起きてから原因を調査し、再発予防を呼びかける方法が主流でした。しかし、それだけでは潜在的なリスクを放置した状態となり、根本的な予防ができない点が問題視されていました。
リスクアセスメントは予測しうるリスクを多角的に分析してから対策方法とともに情報を共有します。危険と思われる箇所や作業方法、作業時の姿勢などについてピックアップしながら対策を講じていくので、事故の発生予防に効果が期待できるのです。
リスクアセスメントの進め方
リスクアセスメントの進め方は、はじめに2つのステップで実施要領を決定します。
- リスクアセスメント実施を決定する
- リスクアセスメントの管理者・担当者を決定する
- リスクの大きさを評価するための要素を決定する
- 要素ごとにリスクレベルを決定する
リスクの大きさを評価するための要素とは、危害のひどさ(重篤度)や危険源にさらされる頻度(危険性又は有害性に近づく頻度)、危害回避の可能性(発生の可能性)などです。
リスクレベルとは「致命傷・重篤・中度・軽度」といった被害の重篤度や、「可能性大・可能性中・可能性小」などの発生可能性です。
リスクレベルの評価に使用する手法、様式を決めてから、以下の5つのステップに分けて進めます。(※)
- 危険性を洗い出す
- 危険性ごとのリスクを見積もる
- リスク回避の優先順位を検討する
- 優先順位に応じて対応する
- 対応した結果を記録する
ここからは5つのステップに沿ってリスクアセスメントの方法をみていきましょう。
※参照元:厚生労働省「職場のリスクアセスメントQ&A」
ステップ①危険性を洗い出す
はじめに、職場や作業における危険性を洗い出します。
機械・設備・作業内容・環境・取り扱っている物質などの危険性・有害性を特定していきます。情報源として次の事例やフィードバックを活用しましょう。
- 前年度までの災害発生状況
- ヒヤリ・ハット事例
- 作業手順・作業マニュアル
- 同業他社などの事故災害事例
- 専門家によるフィードバック
- 従業員から寄せられた要望や意見
- 安全施工サイクルなど
実際に起きた事故災害のほかにも、現場で働いている従業員や外部の専門家からのフィードバックも参考になります。また、厚生労働省が提供している「作業別モデル対策シート」を使用して、危険な行動や対策の抜け漏れを洗い出すこともできます。(※)
※参照元:厚生労働省 職場のあんぜんサイト「作業別モデル対策シート」
ステップ②危険性ごとのリスクを見積もる
次に、洗い出した危険性ごとにリスクを見積もります。
加算法は、危害のひどさ(重篤度)や危険源にさらされる頻度(危険性又は有害性に近づく頻度)、危害回避の可能性(発生の可能性)にそれぞれ照らし合わせて、どの程度リスクが高いかを判断します。
- 危害のひどさ(重篤度)
- 危険源にさらされる頻度(危険性又は有害性に近づく頻度)
- 危害回避の可能性(発生の可能性)
リスクの見積もり方には「加算法」「マトリクス法」「リスクグラフ法」といった手法があります。数値やマトリクスを用いて、客観的に危険度を評価しましょう。
ステップ③リスク回避の優先順位を検討する
見積もったリスクのうち、すぐにリスク回避が必要なものから軽微なものまでに優先順位をつけていきます。
死亡や致命傷の可能性が高いもののように、即時改善・回避をとらなければならないものを最優先事項としてください。
ステップ④優先順位に応じて対応する
ステップ③で順位付けをしたものから、順番に対応策を実施します。
厚生労働省では、法令に定められた事項がある場合は、その事項を実施することを前提として、次の優先順位で可能なかぎり高い順位のものを実施すべきとしています。(※)
- 危険な作業の廃止・変更等、設計や計画の段階から労働者の就業に係る危険性又は有害性を除去又は低減する措置
- 工学的対策(安全装置・局所排気装置・防音囲いの設置等)
- 管理的対策(マニュアル整備・立ち入り禁止措置の実施・ばく露管理・教育訓練の実施等)
- 個人的保護具の使用(1〜3を講じても除去や低減できないリスクに対して実施する)
死亡事故のように重大な事故災害のおそれがあるものは、法令にしたがって対策を実施することを前提に、1〜4の順番で低減措置を実施しましょう。
※参照元:厚生労働省 職場のあんぜんサイト「リスク低減措置の優先順位」
ステップ⑤対応した結果を記録する
優先順位に応じて対処した内容と結果を記録します。結果をデータとして残すことで、次回のリスクアセスメントに役立てられるほか、改善点を洗い出してさらに効果的な対策方法に繋げられます。
リスクアセスメントの代表的な手法
リスクアセスメントにはいくつかの手法があります。3つの代表的な手法である「加算法」「マトリクス法」「リスクグラフ法」を確認していきましょう。
加算法
加算法は、危害のひどさ(重篤度)や危険源にさらされる頻度(危険性又は有害性に近づく頻度)、危害回避の可能性(発生の可能性)といった項目にリスクを照らし合わせて、複数の段階から点数を足し合わせていき、合計点数を算出する方法です。
【加算法の例:危害のひどさ(重篤度)】
点数 | 危害のひどさ |
10点 | 重大 |
6点 | 重症 |
3点 | 軽症 |
1点 | 軽微 |
【加算法の例:危険源にさらされる頻度(危険性又は有害性に近づく頻度)】
点数 | 危険源にさらされる頻度 |
4点 | 頻繁 |
2点 | 時々 |
1点 | まれ |
【加算法の例:危害回避の可能性(発生の可能性)】
点数 | 危害回避の可能性 |
6点 | ほとんどない |
4点 | 可能性あり |
2点 | 可能性が高い |
1点 | 確実 (危険は容易に回避できる/容易に検知できる) |
【加算法の例:合計点数とリスクレベル】
リスクレベル | 加算値 | リスクの判断 |
4 | 12〜20点 | 極めて重大 |
3 | 8〜11点 | 重大な問題がある |
2 | 5〜7点 | 多少問題がある |
1 | 3〜4点 | 些細なリスクがある |
複数の項目ごとに点数を割り振り、加算しながら合計していきます。リスクレベルとして4段階などに分けて、どの程度のリスクかを判断します。
マトリクス法
マトリクス法(マトリックス法/リスクマトリックス法)は危害のひどさと発生の可能性をそれぞれ段階に分け、テーブルに割り振って2種類のパラメータを組み合わせる方法です。
危害のひどさ、発生の可能性をそれぞれ4段階で評価した場合、次のようになります。
【マトリクス法の例】
危害のひどさ (特に重大) | 危害のひどさ (重大) | 危害のひどさ (中程度) | 危害のひどさ (軽微) | |
発生の可能性 | Ⅰ | Ⅰ | Ⅰ | Ⅱ |
発生の可能性 | Ⅰ | Ⅰ | Ⅱ | Ⅲ |
発生の可能性 | Ⅰ | Ⅱ | Ⅲ | Ⅳ |
発生の可能性 | Ⅲ | Ⅲ | Ⅲ | Ⅳ |
上記のような2つのパラメータ以外に、3つや4つのパラメータでリスクを判断する方法もあります。
リスクの程度をさらに細分化するときは、パラメータを増やして判断すると良いでしょう。
リスクグラフ法
リスクグラフ法は、リスクを4つのパラメータに分けながら、総合的なリスク指数を判断する方法です。(※)
【リスクグラフ法の例】
リスクグラフ法は、危険な事象が発生したとき、ただちに起こる危害リスクの評価に適しています。騒音や振動のような慢性的・長期的な危害リスクには適していないため注意が必要です。
※参照元:厚生労働省「機械設備のリスクアセスメントマニュアル 機械設備製造者用」
【業種別】リスクアセスメントのポイント
リスクアセスメントを実施するうえで、業種ごとのポイントをみていきましょう。
製造業
ものづくりに携わる製造業では、大型の機械設備や高熱・高圧など危険性の高い設備を扱うことがあり、有害物質の取り扱いや肉体的に負担のかかる作業も多くみられます。巻き込まれやはさまれ、有害物質の吸引といった労働災害の発災リスクが高く、リスクアセスメントを定期的に実施・周知することが大切です。
建設業
屋外の高所や難所での作業、大型の重機や工具を取り扱うことが多い建設業では、転落・転倒・ケガに注意が必要です。特に高温多湿な時期には熱中症のリスクが高く、体調不良から転落やケガに繋がるおそれもあるため、二次災害の発生も予防を心掛けましょう。
福祉介護業
移乗や入浴介助、更衣や送迎といった力作業をともなう福祉介護業では、肉体にかかる負担を中心にリスクアセスメントを行う必要があります。また、階段や段差で滑ったり転倒したりする可能性や使用中の器具・機械設備の事故災害リスクも洗い出しましょう。
医療業
医療器具や医療設備、介護・介助などを行う医療業では、現場ごとにリスクアセスメントを実施することが大切です。職場や作業の中で身体に被害がかかるリスクを挙げていき、消毒剤や化学物質による健康被害、病原体による感染などの被害も想定する必要があります。
保育・学校
教育施設でも環境や重量物の影響による健康被害のリスクがあります。遊具、ピアノなどの重量物、園内や校内の機械設備による事故災害のほか、環境的な要因として騒音や高温多湿な環境、周辺にある工場や設備の影響も考慮し、リスクアセスメントを行いましょう。
事務作業
デスクワークとして知られている事務作業ですが、環境や設備、作業内容によっては事故災害のおそれがあります。重量物の運搬やシュレッダーの操作、ハサミ・カッターの使用など細かい作業にもリスクが隠れています。その他、ケーブルや段差による転倒、冷暖房器具や照明に長時間当たり続けることによる健康被害も意識したいポイントです。
リスクアセスメントの事例
リスクアセスメントの事例として、食料品製造業と木材・木材製品製造業の2例を紹介します。
食料品製造業の事例
肉製品の製造業者において「作業者が肉類の切断機器で材料を切断中、カッターが回転したまま手指を近づけたために、回転体に接触し手指を負傷した」という過去事例からリスクアセスメントを行った事例です。
危害のひどさ(重篤度)や危険源にさらされる頻度(危険性又は有害性に近づく頻度)、危害回避の可能性(発生の可能性)を加算法で判定し、重篤度+頻度+可能性を加算した結果、4段階のリスクレベルでもっとも高い4に相当したため、リスク低減措置の優先順位に沿って内容を検討しました。
作業の廃止は難しいことから、工学的対策として覆いや囲いを取り付け、管理的対策としてマニュアルの整備と教育訓練を実施しました。
木材・木材製品製造業
木材加工業者において、同業他社での事例が多い「切れ・こすれ」の労働災害を参考に、木材加工中に材料が跳ね返ることによる事故について、リスクアセスメントを行った事例です。
危害のひどさ(重篤度)と危害回避の可能性(発生の可能性)をマトリクス法で判定した結果、4段階のリスクレベルで2番目に高いⅡに相当したため、リスク低減措置の優先順位に沿って内容を検討しました。
作業の廃止や工学的対策が難しいため、管理的対策として治具・工具の使用と、個人的保護具の使用を開始しました。
リスクアセスメントの概要・手順を押さえて災害予防に活かす
今回は、リスクアセスメントの概要や方法、実例や期待できる効果について紹介しました。
リスクアセスメントはあらゆる職場や作業に欠かせないものです。労働に従事する従業員の安全を守り、健康被害を予防するうえで重要な方策です。
実施前には管理者や担当者を選出し、手法や様式の検討を行って、正しいプロセスで実施しましょう。
計測器・測定器のレンタルなら日本マーツ
危険性 |
|
有害性 |
|
リスクを低減するための方法を複数検討し、優先度をつけます。優先度に応じた措置を順に実施し、措置の結果や措置の内容を記録して、災害を防ぐノウハウとして蓄積します。これらのプロセスが、リスクアセスメントと呼ばれる行動です。
労働災害や健康被害は、さまざまな事業所や作業場で発生するおそれがあります。労働安全衛生法では「危険性又は有害性等の調査及びその結果に基づく措置」として、製造業や建設業等の事業者が、リスクアセスメントとその結果に基づく措置を実施する必要があるとして、努力義務を定めています。
※参照元:厚生労働省安全衛生部安全課「危険性又は有害性等の調査等に関する指針」
リスクアセスメントの目的
リスクアセスメントの目的は、職場や仕事における安全・衛生を確保し、労働災害や健康被害を未然に防ぐことです。
事前にリスクを想定・特定することで予防策を講じられるため、不慮の事故やトラブルを防止できるのです。また、職場環境での安全衛生意識向上にも役立ちます。
技術の革新・進展によって、ものづくりの現場では生産工程が多様化し、複雑化しているといわれています。操作の複雑な機械設備を導入した結果、生産性が向上する一方で労働災害や健康被害のリスクも多様化しています。
リスクアセスメントは多様化する作業環境で個々に危険を把握し、予防するための手段でもあります。具体的にどのような効果が期待できるのでしょうか。
リスクアセスメントを実施することで期待できる効果
リスクアセスメントを実施すると、次の効果が期待できます。
- 職場に潜むリスクを共有できる
- 従業員の安全意識を高める
- 事故の発生リスクを下げる
ここからは、リスクアセスメントによって得られる効果を確認していきましょう。
職場に潜むリスクを共有できる
労働や作業においてどのようなリスクがあるのかを洗い出し、特定・周知ことで、潜在的なリスクを従業員全員が共有できます。
一例として、有害な化学物質を扱う作業場では、化学物質の特性や危険性、事故につながりやすい行動などをまとめたうえで、注意すべきポイントを明らかにします。その情報を従業員全員に共有して注意喚起を行うことで、誤った化学物質の取り扱いを未然に防ぎ、労働災害や健康被害を予防できるという仕組みです。
過去に発生した労働災害や健康被害の内容、同業他社の発災事例を参考にリスクを共有する手法も有効です。今まで意識されていなかった、または見落とされていたリスクを共有することができます。
従業員の安全意識を高める
目の前の作業に取り掛かっているあいだは、災害や事故の発生リスクに気づきにくいものです。そこで、事前にリスクアセスメントを行うことで、従業員一人ひとりや従業員同士での安全意識を高められます。
リスクアセスメントのポイントは、分析者が全員で参加し、管理者から従業員まで全員が同じ認識をもつことです。リスクを明確にして対策をするだけではなく、全員が当事者としての意識をもつことが、トラブルの予防に繋がるのです。
危険な作業や危険物を扱う環境では、過去に発生した災害や事故の事例を周知する方法も意識の向上に役立ちます。方法や取り扱いを誤ると重大な傷病、または命を失うおそれもあると把握することで、安全意識をもちながら業務に取り掛かれるでしょう。
事故の発生リスクを下げる
リスクを従業員全員で共有し、個々の安全意識が向上することで、事故の発生リスクを下げる効果が期待できます。
一人ひとりがリスクを理解し、避けようと予防するようになり、従業員同士の声掛けや情報共有の機会も生まれます。
これまで、労働災害や健康被害を防止する方法は事故が起きてから原因を調査し、再発予防を呼びかける方法が主流でした。しかし、それだけでは潜在的なリスクを放置した状態となり、根本的な予防ができない点が問題視されていました。
リスクアセスメントは予測しうるリスクを多角的に分析してから対策方法とともに情報を共有します。危険と思われる箇所や作業方法、作業時の姿勢などについてピックアップしながら対策を講じていくので、事故の発生予防に効果が期待できるのです。
リスクアセスメントの進め方
リスクアセスメントの進め方は、はじめに2つのステップで実施要領を決定します。
- リスクアセスメント実施を決定する
- リスクアセスメントの管理者・担当者を決定する
- リスクの大きさを評価するための要素を決定する
- 要素ごとにリスクレベルを決定する
リスクの大きさを評価するための要素とは、危害のひどさ(重篤度)や危険源にさらされる頻度(危険性又は有害性に近づく頻度)、危害回避の可能性(発生の可能性)などです。
リスクレベルとは「致命傷・重篤・中度・軽度」といった被害の重篤度や、「可能性大・可能性中・可能性小」などの発生可能性です。
リスクレベルの評価に使用する手法、様式を決めてから、以下の5つのステップに分けて進めます。(※)
- 危険性を洗い出す
- 危険性ごとのリスクを見積もる
- リスク回避の優先順位を検討する
- 優先順位に応じて対応する
- 対応した結果を記録する
ここからは5つのステップに沿ってリスクアセスメントの方法をみていきましょう。
※参照元:厚生労働省「職場のリスクアセスメントQ&A」
ステップ①危険性を洗い出す
はじめに、職場や作業における危険性を洗い出します。
機械・設備・作業内容・環境・取り扱っている物質などの危険性・有害性を特定していきます。情報源として次の事例やフィードバックを活用しましょう。
- 前年度までの災害発生状況
- ヒヤリ・ハット事例
- 作業手順・作業マニュアル
- 同業他社などの事故災害事例
- 専門家によるフィードバック
- 従業員から寄せられた要望や意見
- 安全施工サイクルなど
実際に起きた事故災害のほかにも、現場で働いている従業員や外部の専門家からのフィードバックも参考になります。また、厚生労働省が提供している「作業別モデル対策シート」を使用して、危険な行動や対策の抜け漏れを洗い出すこともできます。(※)
※参照元:厚生労働省 職場のあんぜんサイト「作業別モデル対策シート」
ステップ②危険性ごとのリスクを見積もる
次に、洗い出した危険性ごとにリスクを見積もります。
加算法は、危害のひどさ(重篤度)や危険源にさらされる頻度(危険性又は有害性に近づく頻度)、危害回避の可能性(発生の可能性)にそれぞれ照らし合わせて、どの程度リスクが高いかを判断します。
- 危害のひどさ(重篤度)
- 危険源にさらされる頻度(危険性又は有害性に近づく頻度)
- 危害回避の可能性(発生の可能性)
リスクの見積もり方には「加算法」「マトリクス法」「リスクグラフ法」といった手法があります。数値やマトリクスを用いて、客観的に危険度を評価しましょう。
ステップ③リスク回避の優先順位を検討する
見積もったリスクのうち、すぐにリスク回避が必要なものから軽微なものまでに優先順位をつけていきます。
死亡や致命傷の可能性が高いもののように、即時改善・回避をとらなければならないものを最優先事項としてください。
ステップ④優先順位に応じて対応する
ステップ③で順位付けをしたものから、順番に対応策を実施します。
厚生労働省では、法令に定められた事項がある場合は、その事項を実施することを前提として、次の優先順位で可能なかぎり高い順位のものを実施すべきとしています。(※)
- 危険な作業の廃止・変更等、設計や計画の段階から労働者の就業に係る危険性又は有害性を除去又は低減する措置
- 工学的対策(安全装置・局所排気装置・防音囲いの設置等)
- 管理的対策(マニュアル整備・立ち入り禁止措置の実施・ばく露管理・教育訓練の実施等)
- 個人的保護具の使用(1〜3を講じても除去や低減できないリスクに対して実施する)
死亡事故のように重大な事故災害のおそれがあるものは、法令にしたがって対策を実施することを前提に、1〜4の順番で低減措置を実施しましょう。
※参照元:厚生労働省 職場のあんぜんサイト「リスク低減措置の優先順位」
ステップ⑤対応した結果を記録する
優先順位に応じて対処した内容と結果を記録します。結果をデータとして残すことで、次回のリスクアセスメントに役立てられるほか、改善点を洗い出してさらに効果的な対策方法に繋げられます。
リスクアセスメントの代表的な手法
リスクアセスメントにはいくつかの手法があります。3つの代表的な手法である「加算法」「マトリクス法」「リスクグラフ法」を確認していきましょう。
加算法
加算法は、危害のひどさ(重篤度)や危険源にさらされる頻度(危険性又は有害性に近づく頻度)、危害回避の可能性(発生の可能性)といった項目にリスクを照らし合わせて、複数の段階から点数を足し合わせていき、合計点数を算出する方法です。
【加算法の例:危害のひどさ(重篤度)】
点数 | 危害のひどさ |
10点 | 重大 |
6点 | 重症 |
3点 | 軽症 |
1点 | 軽微 |
【加算法の例:危険源にさらされる頻度(危険性又は有害性に近づく頻度)】
点数 | 危険源にさらされる頻度 |
4点 | 頻繁 |
2点 | 時々 |
1点 | まれ |
【加算法の例:危害回避の可能性(発生の可能性)】
点数 | 危害回避の可能性 |
6点 | ほとんどない |
4点 | 可能性あり |
2点 | 可能性が高い |
1点 | 確実 (危険は容易に回避できる/容易に検知できる) |
【加算法の例:合計点数とリスクレベル】
リスクレベル | 加算値 | リスクの判断 |
4 | 12〜20点 | 極めて重大 |
3 | 8〜11点 | 重大な問題がある |
2 | 5〜7点 | 多少問題がある |
1 | 3〜4点 | 些細なリスクがある |
複数の項目ごとに点数を割り振り、加算しながら合計していきます。リスクレベルとして4段階などに分けて、どの程度のリスクかを判断します。
マトリクス法
マトリクス法(マトリックス法/リスクマトリックス法)は危害のひどさと発生の可能性をそれぞれ段階に分け、テーブルに割り振って2種類のパラメータを組み合わせる方法です。
危害のひどさ、発生の可能性をそれぞれ4段階で評価した場合、次のようになります。
【マトリクス法の例】
危害のひどさ (特に重大) | 危害のひどさ (重大) | 危害のひどさ (中程度) | 危害のひどさ (軽微) | |
発生の可能性 | Ⅰ | Ⅰ | Ⅰ | Ⅱ |
発生の可能性 | Ⅰ | Ⅰ | Ⅱ | Ⅲ |
発生の可能性 | Ⅰ | Ⅱ | Ⅲ | Ⅳ |
発生の可能性 | Ⅲ | Ⅲ | Ⅲ | Ⅳ |
上記のような2つのパラメータ以外に、3つや4つのパラメータでリスクを判断する方法もあります。
リスクの程度をさらに細分化するときは、パラメータを増やして判断すると良いでしょう。
リスクグラフ法
リスクグラフ法は、リスクを4つのパラメータに分けながら、総合的なリスク指数を判断する方法です。(※)
【リスクグラフ法の例】
リスクグラフ法は、危険な事象が発生したとき、ただちに起こる危害リスクの評価に適しています。騒音や振動のような慢性的・長期的な危害リスクには適していないため注意が必要です。
※参照元:厚生労働省「機械設備のリスクアセスメントマニュアル 機械設備製造者用」
【業種別】リスクアセスメントのポイント
リスクアセスメントを実施するうえで、業種ごとのポイントをみていきましょう。
製造業
ものづくりに携わる製造業では、大型の機械設備や高熱・高圧など危険性の高い設備を扱うことがあり、有害物質の取り扱いや肉体的に負担のかかる作業も多くみられます。巻き込まれやはさまれ、有害物質の吸引といった労働災害の発災リスクが高く、リスクアセスメントを定期的に実施・周知することが大切です。
建設業
屋外の高所や難所での作業、大型の重機や工具を取り扱うことが多い建設業では、転落・転倒・ケガに注意が必要です。特に高温多湿な時期には熱中症のリスクが高く、体調不良から転落やケガに繋がるおそれもあるため、二次災害の発生も予防を心掛けましょう。
福祉介護業
移乗や入浴介助、更衣や送迎といった力作業をともなう福祉介護業では、肉体にかかる負担を中心にリスクアセスメントを行う必要があります。また、階段や段差で滑ったり転倒したりする可能性や使用中の器具・機械設備の事故災害リスクも洗い出しましょう。
医療業
医療器具や医療設備、介護・介助などを行う医療業では、現場ごとにリスクアセスメントを実施することが大切です。職場や作業の中で身体に被害がかかるリスクを挙げていき、消毒剤や化学物質による健康被害、病原体による感染などの被害も想定する必要があります。
保育・学校
教育施設でも環境や重量物の影響による健康被害のリスクがあります。遊具、ピアノなどの重量物、園内や校内の機械設備による事故災害のほか、環境的な要因として騒音や高温多湿な環境、周辺にある工場や設備の影響も考慮し、リスクアセスメントを行いましょう。
事務作業
デスクワークとして知られている事務作業ですが、環境や設備、作業内容によっては事故災害のおそれがあります。重量物の運搬やシュレッダーの操作、ハサミ・カッターの使用など細かい作業にもリスクが隠れています。その他、ケーブルや段差による転倒、冷暖房器具や照明に長時間当たり続けることによる健康被害も意識したいポイントです。
リスクアセスメントの事例
リスクアセスメントの事例として、食料品製造業と木材・木材製品製造業の2例を紹介します。
食料品製造業の事例
肉製品の製造業者において「作業者が肉類の切断機器で材料を切断中、カッターが回転したまま手指を近づけたために、回転体に接触し手指を負傷した」という過去事例からリスクアセスメントを行った事例です。
危害のひどさ(重篤度)や危険源にさらされる頻度(危険性又は有害性に近づく頻度)、危害回避の可能性(発生の可能性)を加算法で判定し、重篤度+頻度+可能性を加算した結果、4段階のリスクレベルでもっとも高い4に相当したため、リスク低減措置の優先順位に沿って内容を検討しました。
作業の廃止は難しいことから、工学的対策として覆いや囲いを取り付け、管理的対策としてマニュアルの整備と教育訓練を実施しました。
木材・木材製品製造業
木材加工業者において、同業他社での事例が多い「切れ・こすれ」の労働災害を参考に、木材加工中に材料が跳ね返ることによる事故について、リスクアセスメントを行った事例です。
危害のひどさ(重篤度)と危害回避の可能性(発生の可能性)をマトリクス法で判定した結果、4段階のリスクレベルで2番目に高いⅡに相当したため、リスク低減措置の優先順位に沿って内容を検討しました。
作業の廃止や工学的対策が難しいため、管理的対策として治具・工具の使用と、個人的保護具の使用を開始しました。
リスクアセスメントの概要・手順を押さえて災害予防に活かす
今回は、リスクアセスメントの概要や方法、実例や期待できる効果について紹介しました。
リスクアセスメントはあらゆる職場や作業に欠かせないものです。労働に従事する従業員の安全を守り、健康被害を予防するうえで重要な方策です。
実施前には管理者や担当者を選出し、手法や様式の検討を行って、正しいプロセスで実施しましょう。
計測器・測定器のレンタルなら日本マーツ